Rotational molding is a well-known manufacturing process that enables the production of high-quality plastic products. This process involves heating plastic resins in a mold until they melt and then rotating the mold slowly to allow the molten material to spread and coat the inside walls evenly. Rotational molding, also known as Rotational Molding, is a highly flexible process that can produce parts in various shapes, sizes, and textures, including complex geometries that are difficult or impossible to manufacture with other molding processes. In this article, we will provide you with a complete guide to rotational molding and how it works.
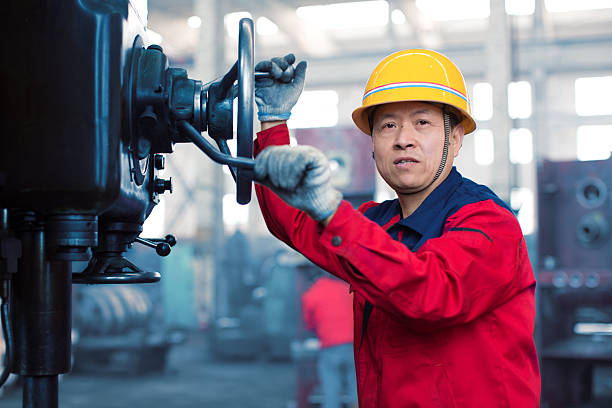
- How Does Rotational Molding Work?
The rotational molding process involves four distinct stages: Loading, Heating, Cooling, and Unloading. First, a measured amount of plastic resin is loaded into the mold, which is then closed and heated in an oven. As the mold rotates slowly, the molten plastic cools and solidifies on the inside walls of the mold to form the desired shape. Once the mold has cooled down to the point where the part is sufficiently solid, it is removed from the oven and cooled by either exposing it to ambient air or submerging it in water. Finally, once the part has reached the designed temperature, it is opened, and the final product is removed.
- Advantages of Rotational Molding
One of the biggest advantages of rotational molding is that it offers a great deal of design flexibility. The process can produce parts in numerous shapes and sizes, including multi-piece assemblies, without the need for expensive tooling. This means that new designs can be tested and manufactured quickly and cost-effectively. Additionally, rotomolded parts have excellent strength-to-weight ratios, making them ideal for applications where lightweight parts are required. Rotomolding is also a low-pressure process, which means that the mold tooling can last longer and that less energy is needed to produce the final parts. Finally, because the process is automated and requires little operator intervention, it is beneficial for high-volume production runs.
- Materials Used in Rotational Molding
The rotational molding process uses a wide range of thermoplastics, including polyethylene, PVC, nylon, polycarbonate, and polypropylene, to name a few. Each material has its unique properties, such as impact resistance, chemical resistance, and UV resistance. The choice of resin depends on several factors, such as the required properties of the final product, the intended application, and the budget. It is important to note that certain materials, such as PVC, may require special handling to avoid negative environmental impacts, and others, like nylon, are better suited for low-volume production runs.
- Applications of Rotational Molding
Rotational molding is used in various industries, including automotive, recreation, marine, and construction. In the automotive industry, rotomolded parts are used for fuel tanks, dashboards, and various other components. In the recreation sector, they are commonly used for kayaks, drums, and coolers. In the marine industry, rotomolding is used for creating buoyancy tanks, marine battery boxes, and access hatches. The construction industry also benefits from rotomolding, as the process can be used to create large tanks, water cisterns, and septic tanks.
- Future of Rotational Molding
Rotational Molding has evolved significantly over the years and is continually advancing towards being more sustainable and environmentally friendly. Many manufacturers are implementing recyclable resins and melting techniques that reduce environmental impacts. With an increasing focus on sustainability, rotomolding is poised to become an essential part of manufacturing in various industries in the future.
In conclusion, rotomolding is a versatile and cost-effective process used in various industries to produce high-quality plastic products. Its advantages include design flexibility, low-pressure processing, and strength-to-weight ratios. The process is also well-suited to producing complex shapes that are difficult to create using other manufacturing processes. While the future of rotomolding looks bright, sustainability is an essential aspect that must be considered in the industry's growth and evolution. This guide has provided you with a comprehensive understanding of the rotational molding process and its benefits, and you can now make an informed decision when selecting manufacturing techniques for your products.